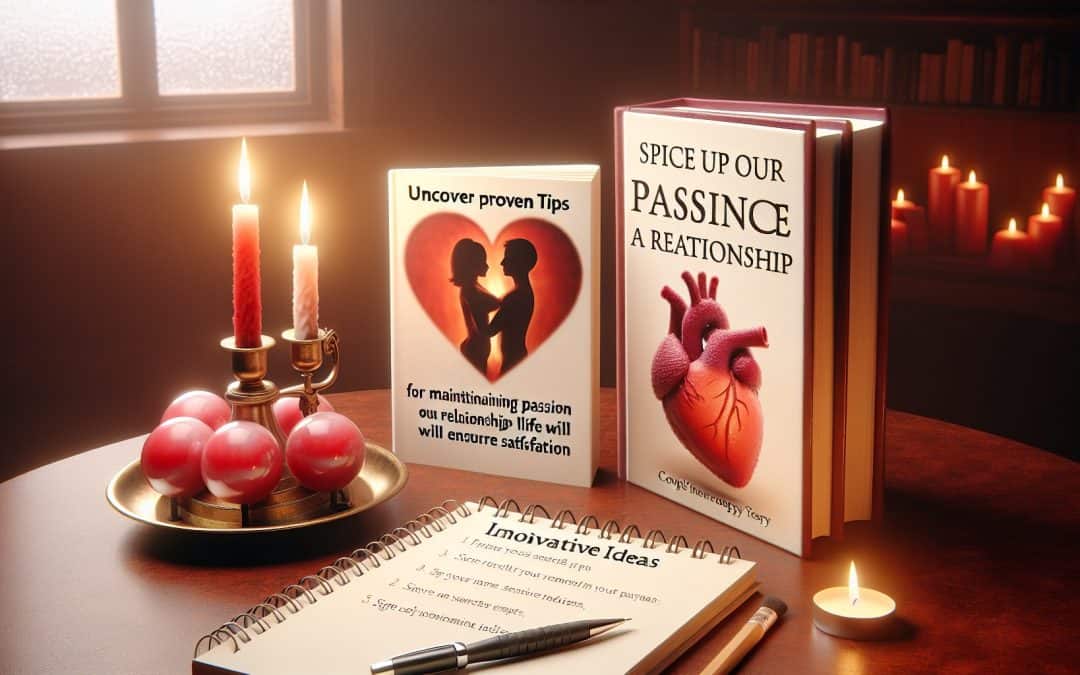
Kako ohraniti strast v zvezi: Nasveti za razburljivo spolno življenje
Osnova vsake močne in strastne zveze tiči v učinkoviti komunikaciji med partnerjema. Iskren pogovor lahko deluje kot čudežno zdravilo, ki ohranja odnos živ in poln strasti. Doseganje globlje povezanos
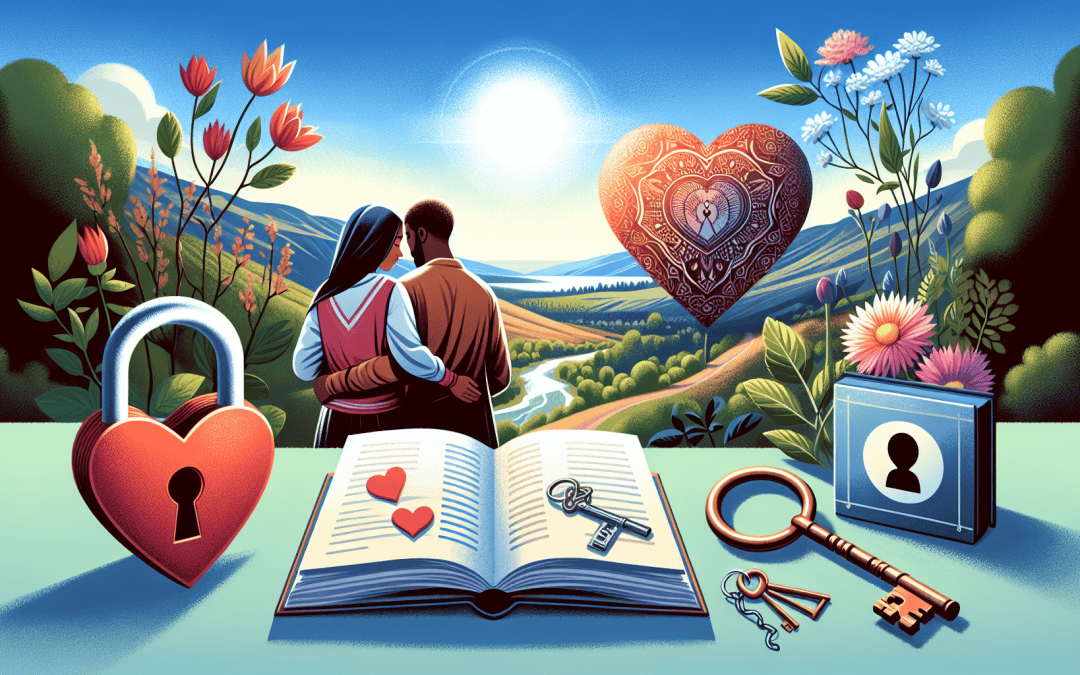
Znaki ljubezni: Kako prepoznati, da te partner resnično ljubi
Znaki ljubezni se pogosto kažejo skozi dejanja, ki so močnejša od besed. Kako prepoznati, da te partner resnično ljubi skozi njegovo vedenje, je vprašanje, ki si ga mnogi zastavljajo v medsebojnih odn
Ohranjanje čustvene povezanosti: Zakaj so redni odnosi s partnerjem ključni?
Ohranjanje čustvene povezanosti z rednimi odnosi s partnerjem je bistvenega pomena za gradnjo in ohranjanje globljega zaupanja v partnerskem odnosu. Zaupanje ni nekaj, kar se pojavi čez noč, temveč se
Pomeni o intimnih pogovorih s partnerjem: Ključ do globljega povezovanja
Intimni pogovori s partnerjem so kot nežno luščenje čebule, kjer vsaka odstranjena plast razkrije bolj ranljiv, a pristnejši del nas samih. Ta proces razkrivanja je srž koncepta, ki ga imenujemo “Pome
Omejitve in prednosti erotičnega telefonskega klepeta v primerjavi s spolnimi sestanki
Erotični telefonski klepet omogoča posameznikom, da svojo intimnost doživljajo na edinstven način, ki se bistveno razlikuje od fizične bližine, ki je značilna za spolne sestanke. Pri tej obliki komuni
Kratek poljub: Zgodbe o ljubezenskih romancih, ki so se končale z enim samim dotikom
Kratki poljubi so pogosto simbol neizrečenih obljub in neskončnih možnosti. V književnosti in resničnem življenju je “Kratek poljub: Zgodbe o ljubezenskih romancih, ki so se končale z enim samim dotik
Skriti biserji: Ljubezenske zgodbe, ki so zasijale le za en trenutek
V zgodovini ljubezni so številne zgodbe, ki jih je čas skoraj povsem izbrisal iz kolektivnega spomina. Med temi so “Skriti biserji: Ljubezenske zgodbe, ki so zasijale le za en trenutek”, ki so
Biseri modrosti: Ljubezen v zlatih letih
Biseri modrosti: Ljubezen v zlatih letih ni zgolj metafora za dolgoletno razmerje, temveč je tudi navodilo, kako ohraniti iskrice ljubezni skozi desetletja skupnega življenja. Ko prečkamo prag zrelih
Mimo preteklosti: Zgodbe o enkratnih ljubezenskih romancah
V podnaslovu “Mimo preteklosti: Zgodbe o enkratnih ljubezenskih romancah in njihovem vplivu na sedanjost” se poglobimo v čustveni svet kratkotrajnih, a intenzivnih romantičnih doživetij. Takšne zgodbe
Erotični telefon in mentalno zdravje: Vpliv na dobro počutje in spolno zadovoljstvo
Uporaba erotičnih telefonskih storitev je v današnjem času postala ena izmed alternativ, ki ljudem pomagajo pri raziskovanju lastne seksualnosti in pri tem pozitivno vpliva na njihovo mentalno zdravje
Umetnost erotičnega telefonskega klepeta: Kako ohraniti vzburjenje na daljavo
Umetnost erotičnega telefonskega klepeta ni le govorjenje o spolnosti z uporabo sugestivnih in provokativnih besed; predstavlja celosten pristop k ustvarjanju senzualne izkušnje, kjer glas postane oro
Vloga komunikacije pri upravljanju spolne napetosti med prijatelji
Razumevanje in izražanje občutkov je kritično pri navigaciji po zapletenih vodah čustvenih in spolnih odnosov med prijatelji. Vloga komunikacije pri upravljanju spolne napetosti med prijatelji se tu p
Meje med seksom in prijateljstvom: Kako se usmerjati skozi kompleksne odnose
Razumevanje in postavljanje meja med seksom in prijateljstvom je ključnega pomena za ohranjanje zdravih in izpolnjujočih odnosov. V svetu, kjer so odnosi vse bolj fluidni in manj definirani, je pomemb
Vpliv spolnega odnosa na prijateljsko vez: Raziskovanje možnih posledic
Dodajanje spolne komponente v prijateljsko vez lahko povzroči pomembne čustvene premike med obema posameznikoma. Takšna preobrazba prijateljstva je pogosto rezultat povečane stopnje intimnosti, ki je
Pomen kompromisa v partnerskem odnosu: Ključ do trajne sreče v zakonu
Kompromis igra ključno vlogo v vsakem partnerskem odnosu, saj predstavlja most, ki povezuje različne poglede, želje in potrebe dveh posameznikov. V odstavku “Pomen kompromisa v partnerskem odnosu: Tem
Iskanje ljubezni: Kje najti svojo sorodno dušo v sodobnem svetu
Iskanje ljubezni v digitalni dobi se marsikomu zdi kot navigacija po neskončnem morju možnosti, kjer lahko v parih klikih srečate nekoga, ki deli vaše zanimanje, vrednote ali pa se preprosto ujame z v
Portali ki zagotavljajo delovanje spletne strani enstroj.si
Poceni vedeževanje
Če do danes niste pomislili na vedeževanje, ker je morda predrago, ali pa mu ne zaupate, kliknite tule pa si boste v trenutku premislili.
Magično vedeževanje
Morda se vam zdi napovedovanje prihodnosti in pogled naprej nekaj neverjetnega in nedoumljivega. Dovolite, da vas o nasprotnem prepričajo naši odlični vedeževalci.
Hitro posojilo
Ko pride trenutek, ko človek nujno potrebuje denar ni časa za omahovanje. Nudimo vam izjemno hitro kreditiranje in zelo malo pogojev.
Vedeževanje 090
Iskanje odgovorov in rešitev še nikoli ni bilo tako hitro in enostavno. Zgolj pokličete enega izmed naših super vedeževalcev ter poskrbite za svoj miren dan.
Vroča linija
Bi naslonil svojo glavo na bogato obdarjeno oprsje in prisluhnil resničnim izpovedim seksi zapeljivk in pohotnic? Klikni in preveri kje in kako!
Hitri kredit
Vas skakanje od banke do banke in čakanje v vrsti utruja? Omislite si hiter spletni kredit, ki je tako enostaven kot bi si v lokalu naročili kavo.
Vedeževanje center
Najboljše vedeževanje in odgovore na svoja vprašanja boste našli tam kjer se nahajajo najboljši vedeževalci. V našem centru vedeževanja seveda!
Vedeževanje prek interneta
Danes je internet del življenja vsakega posameznika zato ne čudi, da so preko spleta na voljo tudi vedeževalci. Super enostavno vedeževanje in natančni odgovori.
Hitri krediti
Brez denarja, ko ga najbolj nujno potrebujete? Kliknite tule in preverite izjemno ponudbo s pomočjo katere lahko do denarja pridete takoj. Ne bo vam žal!
Super vedeževanje
Ko beseda steče o prihodnosti in o tem kako rešiti določene naloge in izzive je jasno nekaj. Po najboljše in najhitrejše odgovore se odpravite k našim vedeževalcem.
Hot line
Ko si zaželiš vroče popestritve in kakšnega orgazma, bo najbolje poklicati na najbolj vročo linijo v naši deželi. Klikni in preveri!
Vedeževanje tarot
Tarot karte niso nič čarovniškega, zgolj orodje v rokah usposobljenih ljudi, ki z njihovo pomočjo razrešijo vaše še tako zapletene težave. Dovolite, da vam priskočijo na pomoč.
Vedeževanje
Vas zanima vedeževanje? Potem nikakor ne zamudite izjemne priložnosti in kliknite tule ter si priskrbite vse odgovore na svoja vprašanja.
090 vedeževanje
Kar preko telefona razrešite vse dvome o tem ali boste dobili novo službo, ali pa glede strahu pred tem, da otrok ne bi uspel izdelati šole. Vprašajte karkoli.
Vedeževanje Slovenija
V Sloveniji je vedeževanje v zadnjem času močno prisotno med nami. K sreči združujemo pod svojim okriljem skupino najbolj nadarjenih vedeževalk in vedeževalcev.
Hitri krediti
Denar ni problem, če ga imaš. Ko pa ti ga primanjkuje ali se pojavi nepredviden strošek pa seveda pomisliš na kredit. Najhitreje do denarja z našo pomočjo!